Philip Whiteman
Well-known
My starting point was a camera with a broken shutter, frozen focus mount, foggy finder and lots of green corrosion where the chromed panels met the leather covering. It was so cheap that I thought I had nothing to lose, so I bought the Peter Tooke repair manual, read all I could find about Contax and Kiev repairs on the Rangefinder Forum, and launched into it.
I won't repeat the advice already given online and in the manual (just go buy a copy, I would say) but there are one or two things that are not mentioned in the book and some accepted online wisdom I would perhaps dispute.
First, the importance of having or being able to produce the correct size screwdriver blades is worth emphasizing: I happened to have an el cheapo bench grinder that allowed me to thin down one blade to remove the large screw in the centre of the rewind knob without marking it, but - more critically - was also useful in reshaping one of my watchmakers screwdrivers to fit the narrow but wide slot in the shutter tensioning spindle.
I thought fitting new tapes was the supreme test of my manual dexterity (the light bulb going on over head moment was realizing that sewing the ends of the tapes was actually easier than attempting to clamp or glue them together temporarily because the thread automatically aligns the join) but almost stalled with the difficulty in tensioning the shutter. Time and again I would wind up the tension only to have the screwdriver blade slip out of engagement and let the shutter unroll. It was only when someone else explained in a FSU RF thread how vital it was to use a correctly sized blade that the penny dropped. I ground back the tip of a driver that was the right width but otherwise too thin and that did the trick - suddenly it was possible!
Neither the Tooke manual nor the various online instructions identify precisely how the low speed escapements operate. Beware that the mystery spring attached to the shutter tension latch controls one of these, and if this spring comes adrift (it wraps around a screw head you cannot access without removing the shutter crate from the body) you may suffer random engagement of one escapement and inconsistent shutter speed. In my camera this escapement was gummed up and it was only when I attempted to turn the screw that I found it was supposed to move bodily up and down, and I twigged what was wrong. Freeing up and lubricating this part of the mechanism was the final step in getting the shutter back to near normal operation.
Near normal? Having first over-tensioned the shutter to get the low speeds working, I found it was coming unlatched on one side due to the load on the pins. In the end, I settled for an empirical approach of winding up the tension in stages until the high speeds looked about right in a visual comparison with my Leica R4's electronically-controlled (and presumably dead accurate) shutter. This left the low speeds running sluggishly, which I think is the compromise you have to put up with if you are unable to completely dismantle and properly lubricate the escapements as the professionals are able to do.
Those same professionals would probably shudder in horror at the way I worked the focus mount loose with as much force as I dared apply and then, without dismantling it and disturbing the rangefinder alignment, applied to the exposed helix... er, grease from an espresso machine service kit. (In my defense, I would point out that this stuff doesn't creep and the ploy worked, because the focus action is now beautifully smooth and even.)
Removing the viewfinder optics and cleaning the glass is relatively easy and you get a very good result even without disturbing the moving rangefinder optic and risking it coming adrift and going out of alignment.
Proof of the pudding has just arrived with test film no.1 and a set of negatives and prints that show correct exposures at 125th to 1250th and my guesstimated 30th (50th setting) and 10th (25th setting). The frames were correctly spaced and there's no sign of any light leak.
According to some sources, this should not be: I used Aki-Asahi silk ribbons which some claim are too thin to provide the right friction to maintain the shutter slit width at the higher speed settings. The ribbons in the camera, possibly originals but there is no way of being sure of this, were 0.012" thick. The replacement ones are much thinner - 0.006" - but there's not the slightest sign of shutter tapering. I think that the more serious error would have been to fit Kiev ribbons, which are thicker and would slow the top curtain's travel at low speed settings. Whatever; the Aki-Asahi ribbon just seems to work.
So it can be done by an amateur, but take it from me; it's a steep learning curve, even with the manual to hand, and you are never going to get the perfect result a professional repairman would achieve. Having said that, for all the frustration along the way, there is huge satisfaction in having turned a piece of junk into a working camera.
I won't repeat the advice already given online and in the manual (just go buy a copy, I would say) but there are one or two things that are not mentioned in the book and some accepted online wisdom I would perhaps dispute.
First, the importance of having or being able to produce the correct size screwdriver blades is worth emphasizing: I happened to have an el cheapo bench grinder that allowed me to thin down one blade to remove the large screw in the centre of the rewind knob without marking it, but - more critically - was also useful in reshaping one of my watchmakers screwdrivers to fit the narrow but wide slot in the shutter tensioning spindle.
I thought fitting new tapes was the supreme test of my manual dexterity (the light bulb going on over head moment was realizing that sewing the ends of the tapes was actually easier than attempting to clamp or glue them together temporarily because the thread automatically aligns the join) but almost stalled with the difficulty in tensioning the shutter. Time and again I would wind up the tension only to have the screwdriver blade slip out of engagement and let the shutter unroll. It was only when someone else explained in a FSU RF thread how vital it was to use a correctly sized blade that the penny dropped. I ground back the tip of a driver that was the right width but otherwise too thin and that did the trick - suddenly it was possible!
Neither the Tooke manual nor the various online instructions identify precisely how the low speed escapements operate. Beware that the mystery spring attached to the shutter tension latch controls one of these, and if this spring comes adrift (it wraps around a screw head you cannot access without removing the shutter crate from the body) you may suffer random engagement of one escapement and inconsistent shutter speed. In my camera this escapement was gummed up and it was only when I attempted to turn the screw that I found it was supposed to move bodily up and down, and I twigged what was wrong. Freeing up and lubricating this part of the mechanism was the final step in getting the shutter back to near normal operation.
Near normal? Having first over-tensioned the shutter to get the low speeds working, I found it was coming unlatched on one side due to the load on the pins. In the end, I settled for an empirical approach of winding up the tension in stages until the high speeds looked about right in a visual comparison with my Leica R4's electronically-controlled (and presumably dead accurate) shutter. This left the low speeds running sluggishly, which I think is the compromise you have to put up with if you are unable to completely dismantle and properly lubricate the escapements as the professionals are able to do.
Those same professionals would probably shudder in horror at the way I worked the focus mount loose with as much force as I dared apply and then, without dismantling it and disturbing the rangefinder alignment, applied to the exposed helix... er, grease from an espresso machine service kit. (In my defense, I would point out that this stuff doesn't creep and the ploy worked, because the focus action is now beautifully smooth and even.)
Removing the viewfinder optics and cleaning the glass is relatively easy and you get a very good result even without disturbing the moving rangefinder optic and risking it coming adrift and going out of alignment.
Proof of the pudding has just arrived with test film no.1 and a set of negatives and prints that show correct exposures at 125th to 1250th and my guesstimated 30th (50th setting) and 10th (25th setting). The frames were correctly spaced and there's no sign of any light leak.
According to some sources, this should not be: I used Aki-Asahi silk ribbons which some claim are too thin to provide the right friction to maintain the shutter slit width at the higher speed settings. The ribbons in the camera, possibly originals but there is no way of being sure of this, were 0.012" thick. The replacement ones are much thinner - 0.006" - but there's not the slightest sign of shutter tapering. I think that the more serious error would have been to fit Kiev ribbons, which are thicker and would slow the top curtain's travel at low speed settings. Whatever; the Aki-Asahi ribbon just seems to work.
So it can be done by an amateur, but take it from me; it's a steep learning curve, even with the manual to hand, and you are never going to get the perfect result a professional repairman would achieve. Having said that, for all the frustration along the way, there is huge satisfaction in having turned a piece of junk into a working camera.
marcr1230
Well-known
Nice work!
R
rick oleson
Guest
"Sluggish slow speeds" .... if you're referring to the fact that the shutter wheezes and runs slowly at the slow speeds, this is normal in a prewar Contax. Since the curtains travel together as a unit, in order to hold open for 1/2 second it needs to not only have a very large slit width (the upper curtain winds way up while the lower one is held in position in front of the film during winding), but also a very slow travel speed. If you tension the springs up in an attempt to make the slow speeds sound like a 'normal' camera, nothing will work right.
http://rick_oleson.tripod.com/index-92.html
I've rebuilt many Contax II and III cameras using 1/8" ribbon from Jo Ann fabrics (we didn't always have eBay and Russian suppliers). It's thicker than the original, but a slight amount of extra tension on the springs adjusts for the increased friction. They're not as fussy as their reputation (mostly coming from people who have never worked on one) suggests.
http://rick_oleson.tripod.com/index-92.html
I've rebuilt many Contax II and III cameras using 1/8" ribbon from Jo Ann fabrics (we didn't always have eBay and Russian suppliers). It's thicker than the original, but a slight amount of extra tension on the springs adjusts for the increased friction. They're not as fussy as their reputation (mostly coming from people who have never worked on one) suggests.
Grytpype
Well-known
I think I may have said some nasty things about Aki Asahi ribbons in the past, but like Philip, I recently tried them in a Contax II (wihout adjusting the friction slots). I have the first roll of film still in the camera, but on my shutter tester there was no sign of "inapproprate slippage". I think the extra width of the A-A ribbon may add some friction at the edges. I agree with Rick that the thickness is perhaps not as critical as some think.I used Aki-Asahi silk ribbons which some claim are too thin to provide the right friction to maintain the shutter slit width at the higher speed settings.
Steve.
Philip Whiteman
Well-known
Rick: I must say your online advice was very useful and confidence inspiring. Thank you!
I cannot help but think the ribbon thickness only becomes significant at lower shutter speeds: at high speeds the upper curtain is wound only a few millimeters further on than the lower one, so the difference in tension between the lower curtain roller and the ribbon spools driving the upper curtain is minimal. You do not need much friction to prevent the upper curtain catching the lower one.
It has to only be at lower speeds, when the lower curtain snaps down and the ribbons pulling down the upper curtain slip through slots in the now stationary lower curtain that ribbon thickness can play a significant role in actual shutter speed/exposure time.
I think that it is for this reason that if either the ribbons are too thick (Kiev ribbon in a Contax shutter) or the escapement(s) is/are sticky and running slow (because it's difficult to fully clean and re-lubricate them) one may be tempted to over-tensioni the shutter to get correct low speeds and end up with either the capping latches parting (my experience) or excessive force opening up the gap between the curtains and effectively giving slower speeds at the top end (as professional repairers like Henry G claim).
I took a very conservative approach of only winding on as much tension as was required to match the visual impression of my R4's vertically-running electronic shutter (and yes; you have to close your ears to the very different sound of a Copal/Seiko type shutter and the Contax's fabulous wheezing roll-top desk!)
I cannot help but think the ribbon thickness only becomes significant at lower shutter speeds: at high speeds the upper curtain is wound only a few millimeters further on than the lower one, so the difference in tension between the lower curtain roller and the ribbon spools driving the upper curtain is minimal. You do not need much friction to prevent the upper curtain catching the lower one.
It has to only be at lower speeds, when the lower curtain snaps down and the ribbons pulling down the upper curtain slip through slots in the now stationary lower curtain that ribbon thickness can play a significant role in actual shutter speed/exposure time.
I think that it is for this reason that if either the ribbons are too thick (Kiev ribbon in a Contax shutter) or the escapement(s) is/are sticky and running slow (because it's difficult to fully clean and re-lubricate them) one may be tempted to over-tensioni the shutter to get correct low speeds and end up with either the capping latches parting (my experience) or excessive force opening up the gap between the curtains and effectively giving slower speeds at the top end (as professional repairers like Henry G claim).
I took a very conservative approach of only winding on as much tension as was required to match the visual impression of my R4's vertically-running electronic shutter (and yes; you have to close your ears to the very different sound of a Copal/Seiko type shutter and the Contax's fabulous wheezing roll-top desk!)
R
rick oleson
Guest
Hi Philip: I can't really say. If the ribbons are a bit on the thick side, as mine generally have been, a couple of extra turns of spring tension even out the difference (my notes indicate 12 turns, I think the factory setting was 9). Beyond that, I have never had any issues with incorrect speeds anywhere in the range.
I am dubious of advice from professional Contax repairers named Henry. One of these has written things that were such flamboyantly egregious BS that I have no interest in hearing his opinions on any other Contax-related subject and prefer to trust my own experience, common sense and input from people with larger expertise and smaller ego.
I am dubious of advice from professional Contax repairers named Henry. One of these has written things that were such flamboyantly egregious BS that I have no interest in hearing his opinions on any other Contax-related subject and prefer to trust my own experience, common sense and input from people with larger expertise and smaller ego.
Chubberino
Well-known
Hi Philip: I can't really say. If the ribbons are a bit on the thick side, as mine generally have been, a couple of extra turns of spring tension even out the difference (my notes indicate 12 turns, I think the factory setting was 9). Beyond that, I have never had any issues with incorrect speeds anywhere in the range.
I am dubious of advice from professional Contax repairers named Henry. One of these has written things that were such flamboyantly egregious BS that I have no interest in hearing his opinions on any other Contax-related subject and prefer to trust my own experience, common sense and input from people with larger expertise and smaller ego.
Yup, he put me off to repairs with him.
Frontman
Well-known
I bought a IIA with a bad shutter for a bargain price, but after opening the camera and reading about what was involved, i decided not to attempt the repair. I sent the camera to Oleg in the Ukraine, and he did a beautiful job on it, and for a good price. I have replaced curtains and ribbons on old FSU and Nikon rangefinders, but don't yet have the desire to dig into a Contax.
Philip Whiteman
Well-known
I respect your opinion, Rick and should have said how useful your own site and advice was in getting my Contax running. Yours was the only source that made it clear how to stitch the ribbons correctly, and it worked like a charm. Thank you for putting your notes and drawings online.
R
rick oleson
Guest
I bought a IIA with a bad shutter for a bargain price, but after opening the camera and reading about what was involved, i decided not to attempt the repair. I sent the camera to Oleg in the Ukraine, and he did a beautiful job on it, and for a good price. I have replaced curtains and ribbons on old FSU and Nikon rangefinders, but don't yet have the desire to dig into a Contax.
Hi Frontman: If you've serviced a Kiev, the Contax II and III will be nothing new. The IIa and IIIa, however, are another thing entirely. They're wonderful cameras when everything is in tip top shape, but can be very frustrating when it's not.
R
rick oleson
Guest
I respect your opinion, Rick and should have said how useful your own site and advice was in getting my Contax running. Yours was the only source that made it clear how to stitch the ribbons correctly, and it worked like a charm. Thank you for putting your notes and drawings online.
No problem! They're there to save the old cameras from the dustbin if possible. I have a more complete set than what's online, if you'd like me to email them to you (unless I already have - memory gets slippery these days)
rick
Philip Whiteman
Well-known
I am happy to take you up on that kind offer, Rick.
One observation: post repair, my Contax's slow speeds seem to be picking up with use - perhaps some of the watch oil I applied finding its way fully into the works?
And one question: both the Contax and the Kievs I worked on prior to attempting to fix the German camera have the same brass shim washer at the top of the sprocket. This component - actually a light seal - is easily trapped between the shutter crate and camera body, or between the frame mask and top plate, bending it out of shape. Looking at it closely, it seems to actually be D shaped, and I assumed this is to allow it to be rotated away from the shutter crate/body join when reinstalling the shutter unit. Rotating it back so the flat aligns with the join between frame mask and top plate allows the latter to be refitted with pinching the washer - have I got this right? (At least the Contax has no light leak!)
One observation: post repair, my Contax's slow speeds seem to be picking up with use - perhaps some of the watch oil I applied finding its way fully into the works?
And one question: both the Contax and the Kievs I worked on prior to attempting to fix the German camera have the same brass shim washer at the top of the sprocket. This component - actually a light seal - is easily trapped between the shutter crate and camera body, or between the frame mask and top plate, bending it out of shape. Looking at it closely, it seems to actually be D shaped, and I assumed this is to allow it to be rotated away from the shutter crate/body join when reinstalling the shutter unit. Rotating it back so the flat aligns with the join between frame mask and top plate allows the latter to be refitted with pinching the washer - have I got this right? (At least the Contax has no light leak!)
Highway 61
Revisited
And one question: both the Contax and the Kievs I worked on prior to attempting to fix the German camera have the same brass shim washer at the top of the sprocket. This component - actually a light seal - is easily trapped between the shutter crate and camera body, or between the frame mask and top plate, bending it out of shape. Looking at it closely, it seems to actually be D shaped, and I assumed this is to allow it to be rotated away from the shutter crate/body join when reinstalling the shutter unit. Rotating it back so the flat aligns with the join between frame mask and top plate allows the latter to be refitted with pinching the washer - have I got this right? (At least the Contax has no light leak!)
Yes you've got it right. But the camera will benefit from some black foam strips put here as well before you put the shutter cover back. Ditto with putting some around the VF front window and around the eyepiece.
Also, replacing all the crude original light baffles behind the RF swinging element and all over the beamsplitter prism with larger and thicker custom cut black paper pieces is something to consider.
See pics below, from my own Contax II DIY restoration sessions - using some 3mm acetate ribbon bought from my local craft store, which worked just fine, as Rick wrote.
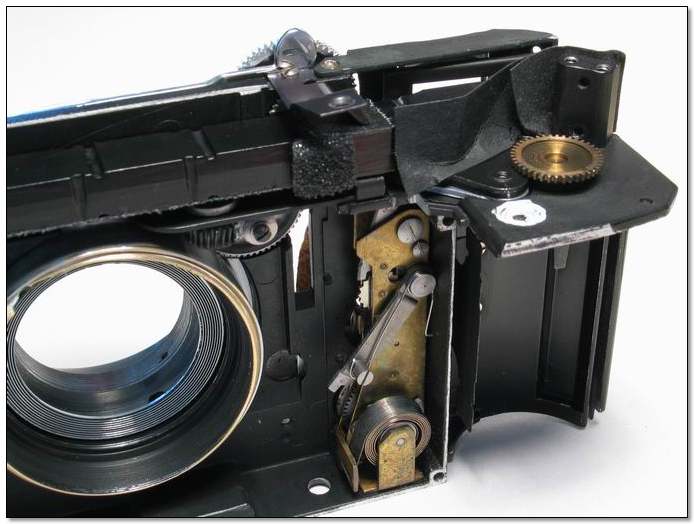
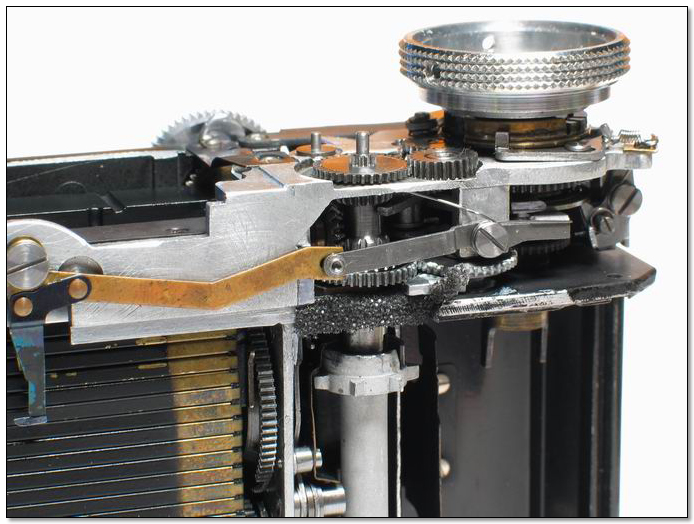
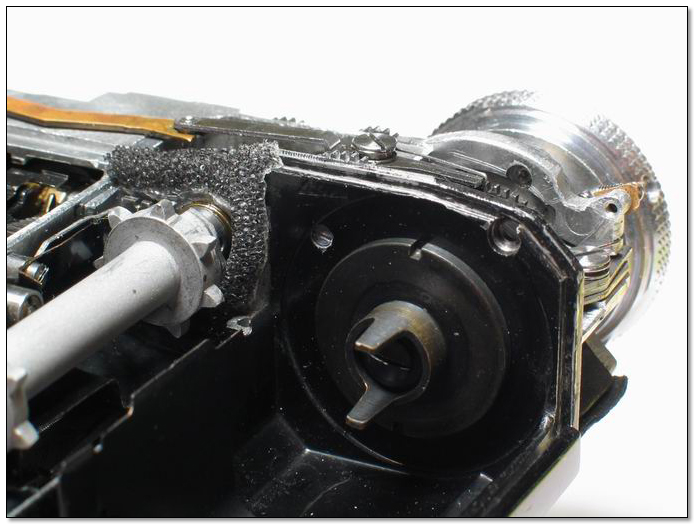
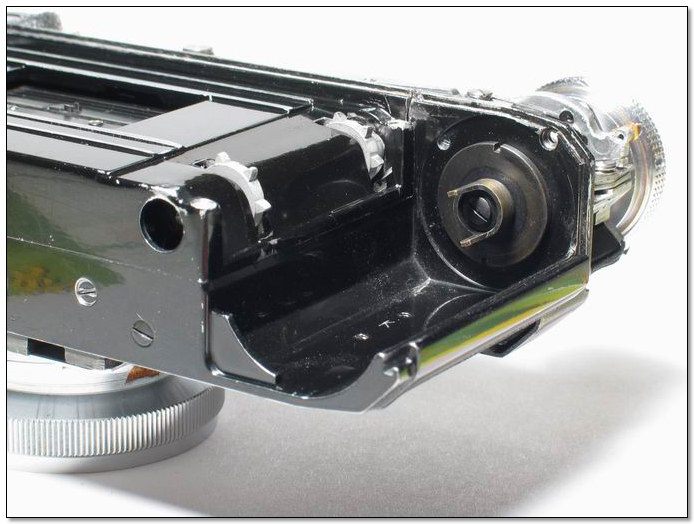
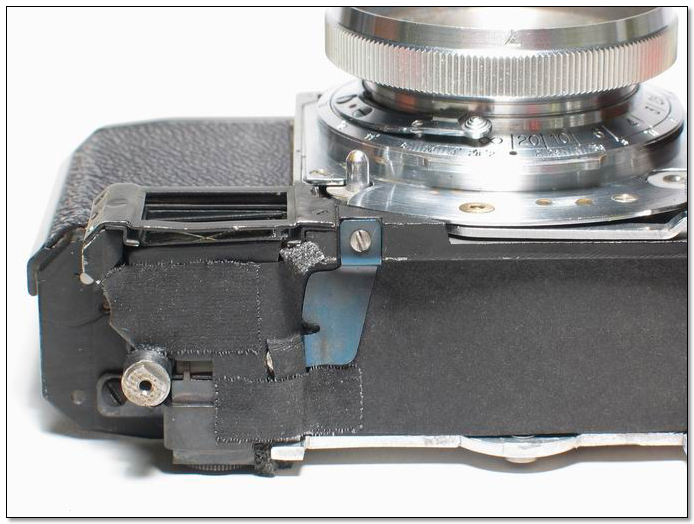
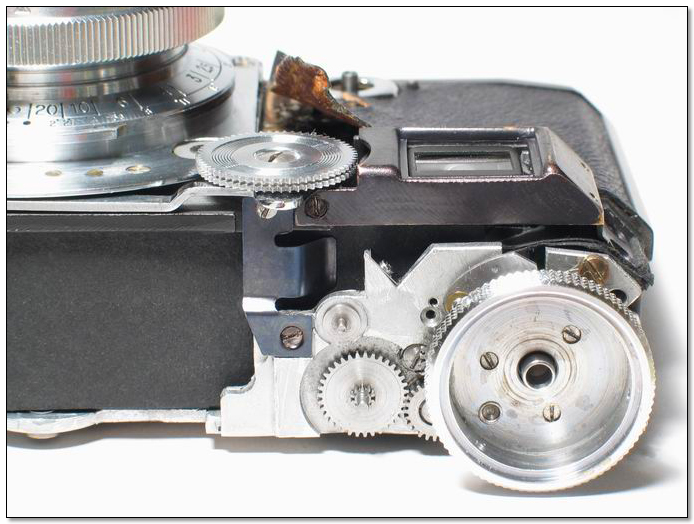
Grytpype
Well-known
The light baffles at the top of the sprocket-spindle seem to be a solution to a problem Zeiss Ikon didn't originally know they had. I haven't seen enough cameras to be certain, but in my rather limited experience, it looks as though the earliest cameras, up to 'B' serials, may have had nothing at all. 'C' serials had the D-washer you describe, and then at some point they added a rather complicated and fragile baffle I've pictured below. I think this normally fitted below the D-washer, but I've seen it above as well. The flat piece to the right (sort-of L-shaped) slides in above the body casting, though my picture of it in place is not very clear. Most Kievs have this baffle as well, but I think some may just have had a larger D-washer. The baffle I've photographed (in a 'G' serial Contax), appears to made of aluminium but I've just repaired one from a Kiev that was made of brass.
I'm not sure where the light leak comes from that these baffles are meant to prevent, but I rather suspect you could live without both and never notice a problem.
As Highway 61 has said, you are dead right about the way to fit the back-casting without damaging the D-washer. They are always badly mutilated. It is very easy to forget to align them properly while assembling.
I'm not sure where the light leak comes from that these baffles are meant to prevent, but I rather suspect you could live without both and never notice a problem.
As Highway 61 has said, you are dead right about the way to fit the back-casting without damaging the D-washer. They are always badly mutilated. It is very easy to forget to align them properly while assembling.


Philip Whiteman
Well-known
Besides refitting the D washer as described, all I did with my Contax was reattach the one corner of the (pretty minimal) black paper light baffle that sits on top the left-hand end of the viewfinder prism. This seems to have done the trick, because there's no light leak visible in any test frames.
I think it became more of an issue with late models Kievs, where the close fit between body and shutter castings became a yawning gap!
I think it became more of an issue with late models Kievs, where the close fit between body and shutter castings became a yawning gap!
Grytpype
Well-known
There are a great variety of light-sealing measures on these cameras. It would be nice to know what they are all for! I just try to replace them as I found them and hope for the best.
Contax always have the paper you mentioned at the left-hand end of the prism. Kievs never have this, but they do have one at the other end covering the gap between the shutter chassis and the prism. Contax never have this.
As well as the long twine running along where the back fits, most cameras also have a short piece fixed to the top-casting. Sometimes this is at the mechanism end, sometimes at the eyepiece end. All very confusing!
Contax always have the paper you mentioned at the left-hand end of the prism. Kievs never have this, but they do have one at the other end covering the gap between the shutter chassis and the prism. Contax never have this.
As well as the long twine running along where the back fits, most cameras also have a short piece fixed to the top-casting. Sometimes this is at the mechanism end, sometimes at the eyepiece end. All very confusing!
Philip Whiteman
Well-known
The stuff you learn on this forum! There's no sign of that wonderfully complicated pressed tin/brass baffle in either of my Kiev 4s, Grytpype (no Thynn?), although they would both have benefitted from one (light leak visible image bottom right/sprocket corner of frame).
I wonder if the thing was supplied as some kind of service fix, rather than a standard factory fit?
I am sure everyone who's posted on this thread so far knows this, but for any newcomer who might be trying to get a recalcitrant Kiev (or Contax) working properly, one further source of useful information on light leaks and much more is the wittily titled Kiev Survival Site http://www3.telus.net/public/rpnchbck/
I wonder if the thing was supplied as some kind of service fix, rather than a standard factory fit?
I am sure everyone who's posted on this thread so far knows this, but for any newcomer who might be trying to get a recalcitrant Kiev (or Contax) working properly, one further source of useful information on light leaks and much more is the wittily titled Kiev Survival Site http://www3.telus.net/public/rpnchbck/
Shafovaloff1
Well-known
I was thinking about slow speeds on the Contax I and for the moment have decided that if 1/2 second was taking 3/4 second and the rest of the slow speeds were within 15-20% of what was intended by Zeiss and the "sports" group were right on I could be happy. And, everything operating consistently otherwise this fit my definition of a user camera.
I am into the engineering physics involved in the design, including the optics. I am buying a more accurate caliper and reading up on how better to use it. How many turns are the rollers at each end designed to have. So I measured the height of the sides and compared that to the thickness of the various supply of "ribbons" "straps" or " belts" used to attach the shutter top and bottom. I suspect that the length for the "ribbons" factored in how many turns around the rollers would be necessary for the design to work, and therefore the thickness of the ribbon. The length of the "ribbon" I measured was 100mm but I do not know whether it was original. Each gear tooth on the top roller moves the top curtain a certain distance but as the roller rolls up the distance per gear tooth also increases a factor for slow speeds, particularly. Also, since my polyester ribbon gets hairy I would expect some resistance formed between the ribbon and shutter, so it might be important to ensure the shutter itself has a smooth surface.
Since there is no instruction book on how to remove the escapements for cleaning I will have to teach myself how to do that...no problem...but in the mean time I will enjoy using these front runners in design of their time.
Thanks to all.
Thomas Shafovaloff
I am into the engineering physics involved in the design, including the optics. I am buying a more accurate caliper and reading up on how better to use it. How many turns are the rollers at each end designed to have. So I measured the height of the sides and compared that to the thickness of the various supply of "ribbons" "straps" or " belts" used to attach the shutter top and bottom. I suspect that the length for the "ribbons" factored in how many turns around the rollers would be necessary for the design to work, and therefore the thickness of the ribbon. The length of the "ribbon" I measured was 100mm but I do not know whether it was original. Each gear tooth on the top roller moves the top curtain a certain distance but as the roller rolls up the distance per gear tooth also increases a factor for slow speeds, particularly. Also, since my polyester ribbon gets hairy I would expect some resistance formed between the ribbon and shutter, so it might be important to ensure the shutter itself has a smooth surface.
Since there is no instruction book on how to remove the escapements for cleaning I will have to teach myself how to do that...no problem...but in the mean time I will enjoy using these front runners in design of their time.
Thanks to all.
Thomas Shafovaloff
Shafovaloff1
Well-known
I am still looking for the tapered pin/screw used to adjust the shutter winding distance and width of "slit" for the high speeds mentioned by Henry Scherer. So far I have taken the winding knob off to view the position of the recesses for the pin to fit but not gone further. And, I have made up my mind to plan each operation involving dismantling to limit wear on the camera parts akin to diminishment of longevity encountered form anesthesia.
Share:
-
This site uses cookies to help personalise content, tailor your experience and to keep you logged in if you register.
By continuing to use this site, you are consenting to our use of cookies.