mooge
Well-known
Some tips on re-silvering and re-cementing a Leica M2 beamspiltter
1. ABSTRACT:
This will be a little (long) write-up on some things I learned while re-silvering my Leica M2's beamsplitter over the summer. All of this was done quite a number of months ago so I'm sure lots of details are missing, but hopefully this is of some use to someone out there. Many cameras have mirrors or cemented optics, so the information presented here may be relevant to other camera-related repairs. As usual, I'm not an expert and with regards to chemistry, I have pretty much no idea what's going on, so don't expect everything I write to be correct.
Apologies if this is somewhat rambling and unprofessional but hey, it's the internet.
2. BACKGROUND:
I have this really beat-up M2 and I drop it all the time for some reason (in fact, it is both the most expensive camera I own and the only one I've dropped... actually I dropped my Pen EE-3 while cycling recently so that last one's not true any more) so I figured it was really only a matter of time before I the prism separated. That came about sometime in spring; I was walking down some stairs and my shoelace strap pulled out on one side and the camera fell. Now I knot the ends twice.
I opened the camera to find that actually two cemented optics had come apart; the beamsplitter and the doublet adjacent to it that directs light from the RF / framelines. Not a big deal. The real problem arose when I was messing with the prisms and decided to stick them together with water-- this quickly dissolved the aluminum semi-silvering of the beamsplitter. Now you know what not to do.
3. METHODS OF SILVERING:
There are a few ways you can silver glass. In the factory, it was done by chemical vapour deposition (CVD). CVD involves placing the item to be silvered in a vacuum chamber, where some aluminum (or gold or whatever) is vapourized and then coats everything in the chamber. This results in a very even layer of deposit, and a near perfect finish. It is possible to make your own CVD apparatus at home, but I don't have a vacuum pump lying around and I can't be trusted with electricity, so I figured the chemical method would be better.
The “old way” of making mirrors (which is essentially what we're doing) is with a reaction of chemical solutions, using silver. There are also various methods to do this; the two that come to mind are the Tollen's reagent reaction and the Rochelle salt method. I chose the Rochelle salt method because it has a longer shelf life and I think the reaction takes a longer time to take place, which would make it easier to control. The disadvantage of these kinds of reactions is that they result in a rather uneven surface. More on this later.
If you don't want to do it yourself, you could send the whole camera to CRR Luton in the UK, who will resilver and rejuvenate the rangefinder of your camera for a reasonable amount (reasonable to me anyways). I would have sent mine in to them (to have it done right!) but they weren't taking in any more repairs for the rest of the year at the time. Also, you could look for companies who could do CVD for you.
4. METHODS OF CEMENTING
Two main choices here: UV-curing optical cement, used on modern optics, or good old Canada balsam, which was notably used on the older Leicas and led to discolouration and finder separation as it aged. I chose Canada Balsam because it's easy to undo if the alignment is off (and it was) and it also has the bonus of smelling really good (it is basically refined tree sap). UV cement, if I recall, requires some pretty nasty solvents to break down. Canada balsam however, takes some time and heat to cure; much longer than the brief exposure to UV light required by the UV cement. UV cement will probably hold up better with age.
The Canada balsam I bought came in a glass jar with a dropper; I didn't see the dropper at first because glass and the balsam have very similar refractive indexes, hence the glass dropper seems to 'disappear' in the balsam. This similarity of refractive index is why balsam is used as an optical cement.
5. REQUIRED MATERIALS:
Canada Balsam
Silver Nitrate
Baking Soda / Soda Ash
Cream of Tartar
Ammonia
Stuff
The weirder things, the balsam and Silver nitrate, were bought from that great flying auction site in the cyberspace (starts with the letter 'E'...). I bought 5g of Silver nitrate for about $20 (and in theory, 5g is plenty ) and 25mL of Canada Balsam for $25.
Ammonia is used as a cleaning fluid and I bought a big bottle of it at Walmart in the cleaning fluids section. Cream of Tartar is some sort of baking thing (don't know much about baking either!) and you should be able to find it at the local Loblaws or equivalent supermarket.
You can buy soda ash (used as a dye stabilizer? I found it at Walmart) if you like or you can be cheap like me and make your own from baking soda. More on this later.
6. THE REACTION:
So after some research on and off the internet, I settled on using the method outlined on this website:
http://www.make-stuff.com/formulas_&_remedies/glass_&_glasses/mirrors.html [1]
Basically, there are two solutions, A and B, which are reacted to deposit silver on your whatever. I changed the quantities of materials to suit my needs (silvering a tiny surface of glass) and this is what I settled on:
A: 1g AgNO3 + NH3
B: 0,2g AgNO3 + 0,2g Rochelle Salt
7. MAKING ROCHELLE SALT:
Rochelle salt (or Potassium Sodium Tartrate, for you IUPAC guys) is pretty cool stuff; you'll find videos online about how you can make giant crystals with it or how it's piezoelectric. Kind of cool, but not really relevant for our purposes. Rochelle salt can be made by mixing Cream of Tartar (Potassium bitartrate) and Soda Ash (Sodium carbonate) together in hot water, straining the mixture, and letting the water evaporate. I can't recall the proportions I used. As mentioned above, I used baking soda instead of soda ash; the baking soda was “baked” for a number of hours in order for it to turn into soda ash. Instructions on how to do this can be found online. I used a candle and a cut-up aluminum can with a shoebox lid as a tray. Not really the safest way to do it but it worked and only a few things caught fire.
8. PREPARING THE SOLUTIONS:
Since I don't have a precise balance or scale, the Rochelle salt and Silver nitrate were measured out using a balance made of Lego. No joke. I hung film cans on each end of the balance with dental floss and used a penny as the reference mass. Since the mass of the penny is known, its placement can be calculated by doing a moment balance; for example, in order to find one gram:
1g x 12,1cm = 2,35g x 5,15cm
Hence if the penny is placed 5,15cm from the pivot of the balance, it will balance with one gram placed 12,1cm from the pivot on the other side.
Obviously, if you have access to a balance accurate to fractions of a gram, that would be more precise.
I made the mistake of using a copper-plated key to scoop silver nitrate out of its little jar. The silver reacts with the copper and I ended up having copper in my silvering solution. Kind of cool to have a copper-coloured mirror but it's probably not good for the end result. How well your silvering turns out depends on how precise and clean you are doing the experiment. I wasn't, and it shows, but despite my sloppiness, I did end up with a workable final product.
Following the instructions from [1]:
A: I put half of the silver nitrate in 100mL, and dropped in ammonia. Nothing happened. Then I added the rest of the silver nitrate. Then it became cloudy. More ammonia – my notes say 40 drops – and it doesn't clear.
B: The silver nitrate and Rochelle salt are mixed in hot water. The solution turns black.
The instructions state that the solutions are to be filtered, but I was too lazy. The precipitate eventually settles at the bottom. Other than what I have in my notes, I don't remember what I did or what happened; it didn't occur according to the instructions though. I kept the solutions in the dark in my camera cabinet and they keep pretty long; I mixed the leftover solutions maybe four months after they were mixed and they silvered the inside of the jar.
9. THE REACTION:
I placed a glass sample in a film can (of course) and poured in roughly half and half of the solutions. Ideally, one would find the time/temperature/concentration combination for a perfect 50/50 semi-silvering; but since this experiment was very rough, the final method was to pour the chemicals, wait and watch. Trial and error. I'd pull the glass out when it looked like it was getting there; if it was too much, I'd wipe the silver off with a finger (it's very easily removed), rinse and try again; or if it was too little I'd put it back in the solution. I found that agitation (swirling) did not help with the reaction (but I can't recall what it did-- uneven coating? Took longer to deposit?).
It's very difficult to get an even coating; especially when it's really half a coating of silver that you want. Keep in mind it's only a few atoms thick for it to pass light through.
It's also difficult to judge when the layer of silver is enough-- too much and your finder will be very dark; too little and you have no rangefinder patch. I had some aluminum left on the prism face (in fact, it wouldn't come off if I scrubbed), and that helped me judge when the silver was appropriately thick. Well, in theory anyways.
If the silver was too thick, it was easily removed by rubbing the surface with a finger. But for some reason, after silvering and cementing and decementing after the silver was found to be too thin, a blotch of silver stuck and would not come off.
Due to contaminants (namely, copper), the silver layer was never really silver. For my first chemical batch, it was a coppery colour, then for the second batch, it was yellowish. These tints will result in a colour cast in the finder.
As an aside, it's quite easy to make a regular (back-silvered) mirror with this method: throw a piece of glass into the solution and wait. Wipe one side, and the other side will be a nice even silver as seen through the glass, despite the unevenness or discolouration of the other (silvered) side. For other photographic uses, front-silvered mirrors are usually used, and again, this tip won't be of much use-- your reflective surface will be the 'difficult' side.
The prism to be silvered for the M2 has three optical faces, with only one requiring silvering. I taped the other surfaces so that they wouldn't be slivered.
10. CEMENTING:
Once you end up with a (barely, in my case) satisfactory semi-silvering, you can stick the beamsplitter together with water and look through it for a basic assessment. And this time, the silvering won't come off. I would look through the beamsplitter and wave a finger by the face where the RF image comes through; if the two images were about equal in brightness, then I'd go ahead for cementing. Or maybe I had it so that the reflected image was brighter? I don't remember. You'll have to experiment.
Tape up the surfaces that you don't want cement on. Apply a small drop of Canada balsam, but enough to ensure that there's enough to cover the entire surface. Then use tape or wire to hold the prisms together with the correct alignment. The correct alignment I found by looking through the beamsplitter and aligning it so that it did not skew the image; so that it was 'straight through' so to speak. Hopefully that makes some sense. In other words, if I was looking at a dot through the beamsplitter, when the beamsplitter was removed, the dot would appear to be in the same place; not above or below.
Curing the cement is usually done in an oven, but I didn't want to waste electricity so I just stuck the cemented assembly on the dashboard of one of our cars whose engine exploded last winter. A couple days in the sun at 60 degrees or more, peak, and it's solid. In fact, I tripped over a tent a couple weeks ago, camera in hand, and the rangefinder is still together and aligned. Before the re-silvering, the RF would lose alignment if you spoke condescendingly in its general direction.
11. DECEMENTING:
If you get it wrong, throw the cemented optics in acetone and they'll come apart quickly. This is also useful for cleaning any balsam that remained from before or removing excess balsam. Note that acetone removes paint, and you'll have to repaint the beamsplitter's non-optic surfaces before it goes back into the camera to reduce stray light.
1. ABSTRACT:
This will be a little (long) write-up on some things I learned while re-silvering my Leica M2's beamsplitter over the summer. All of this was done quite a number of months ago so I'm sure lots of details are missing, but hopefully this is of some use to someone out there. Many cameras have mirrors or cemented optics, so the information presented here may be relevant to other camera-related repairs. As usual, I'm not an expert and with regards to chemistry, I have pretty much no idea what's going on, so don't expect everything I write to be correct.
Apologies if this is somewhat rambling and unprofessional but hey, it's the internet.
2. BACKGROUND:
I have this really beat-up M2 and I drop it all the time for some reason (in fact, it is both the most expensive camera I own and the only one I've dropped... actually I dropped my Pen EE-3 while cycling recently so that last one's not true any more) so I figured it was really only a matter of time before I the prism separated. That came about sometime in spring; I was walking down some stairs and my shoelace strap pulled out on one side and the camera fell. Now I knot the ends twice.
I opened the camera to find that actually two cemented optics had come apart; the beamsplitter and the doublet adjacent to it that directs light from the RF / framelines. Not a big deal. The real problem arose when I was messing with the prisms and decided to stick them together with water-- this quickly dissolved the aluminum semi-silvering of the beamsplitter. Now you know what not to do.
3. METHODS OF SILVERING:
There are a few ways you can silver glass. In the factory, it was done by chemical vapour deposition (CVD). CVD involves placing the item to be silvered in a vacuum chamber, where some aluminum (or gold or whatever) is vapourized and then coats everything in the chamber. This results in a very even layer of deposit, and a near perfect finish. It is possible to make your own CVD apparatus at home, but I don't have a vacuum pump lying around and I can't be trusted with electricity, so I figured the chemical method would be better.
The “old way” of making mirrors (which is essentially what we're doing) is with a reaction of chemical solutions, using silver. There are also various methods to do this; the two that come to mind are the Tollen's reagent reaction and the Rochelle salt method. I chose the Rochelle salt method because it has a longer shelf life and I think the reaction takes a longer time to take place, which would make it easier to control. The disadvantage of these kinds of reactions is that they result in a rather uneven surface. More on this later.
If you don't want to do it yourself, you could send the whole camera to CRR Luton in the UK, who will resilver and rejuvenate the rangefinder of your camera for a reasonable amount (reasonable to me anyways). I would have sent mine in to them (to have it done right!) but they weren't taking in any more repairs for the rest of the year at the time. Also, you could look for companies who could do CVD for you.
4. METHODS OF CEMENTING
Two main choices here: UV-curing optical cement, used on modern optics, or good old Canada balsam, which was notably used on the older Leicas and led to discolouration and finder separation as it aged. I chose Canada Balsam because it's easy to undo if the alignment is off (and it was) and it also has the bonus of smelling really good (it is basically refined tree sap). UV cement, if I recall, requires some pretty nasty solvents to break down. Canada balsam however, takes some time and heat to cure; much longer than the brief exposure to UV light required by the UV cement. UV cement will probably hold up better with age.
The Canada balsam I bought came in a glass jar with a dropper; I didn't see the dropper at first because glass and the balsam have very similar refractive indexes, hence the glass dropper seems to 'disappear' in the balsam. This similarity of refractive index is why balsam is used as an optical cement.
5. REQUIRED MATERIALS:
Canada Balsam
Silver Nitrate
Baking Soda / Soda Ash
Cream of Tartar
Ammonia
Stuff
The weirder things, the balsam and Silver nitrate, were bought from that great flying auction site in the cyberspace (starts with the letter 'E'...). I bought 5g of Silver nitrate for about $20 (and in theory, 5g is plenty ) and 25mL of Canada Balsam for $25.
Ammonia is used as a cleaning fluid and I bought a big bottle of it at Walmart in the cleaning fluids section. Cream of Tartar is some sort of baking thing (don't know much about baking either!) and you should be able to find it at the local Loblaws or equivalent supermarket.
You can buy soda ash (used as a dye stabilizer? I found it at Walmart) if you like or you can be cheap like me and make your own from baking soda. More on this later.
6. THE REACTION:
So after some research on and off the internet, I settled on using the method outlined on this website:
http://www.make-stuff.com/formulas_&_remedies/glass_&_glasses/mirrors.html [1]
Basically, there are two solutions, A and B, which are reacted to deposit silver on your whatever. I changed the quantities of materials to suit my needs (silvering a tiny surface of glass) and this is what I settled on:
A: 1g AgNO3 + NH3
B: 0,2g AgNO3 + 0,2g Rochelle Salt
7. MAKING ROCHELLE SALT:
Rochelle salt (or Potassium Sodium Tartrate, for you IUPAC guys) is pretty cool stuff; you'll find videos online about how you can make giant crystals with it or how it's piezoelectric. Kind of cool, but not really relevant for our purposes. Rochelle salt can be made by mixing Cream of Tartar (Potassium bitartrate) and Soda Ash (Sodium carbonate) together in hot water, straining the mixture, and letting the water evaporate. I can't recall the proportions I used. As mentioned above, I used baking soda instead of soda ash; the baking soda was “baked” for a number of hours in order for it to turn into soda ash. Instructions on how to do this can be found online. I used a candle and a cut-up aluminum can with a shoebox lid as a tray. Not really the safest way to do it but it worked and only a few things caught fire.
8. PREPARING THE SOLUTIONS:
Since I don't have a precise balance or scale, the Rochelle salt and Silver nitrate were measured out using a balance made of Lego. No joke. I hung film cans on each end of the balance with dental floss and used a penny as the reference mass. Since the mass of the penny is known, its placement can be calculated by doing a moment balance; for example, in order to find one gram:
1g x 12,1cm = 2,35g x 5,15cm
Hence if the penny is placed 5,15cm from the pivot of the balance, it will balance with one gram placed 12,1cm from the pivot on the other side.
Obviously, if you have access to a balance accurate to fractions of a gram, that would be more precise.
I made the mistake of using a copper-plated key to scoop silver nitrate out of its little jar. The silver reacts with the copper and I ended up having copper in my silvering solution. Kind of cool to have a copper-coloured mirror but it's probably not good for the end result. How well your silvering turns out depends on how precise and clean you are doing the experiment. I wasn't, and it shows, but despite my sloppiness, I did end up with a workable final product.
Following the instructions from [1]:
A: I put half of the silver nitrate in 100mL, and dropped in ammonia. Nothing happened. Then I added the rest of the silver nitrate. Then it became cloudy. More ammonia – my notes say 40 drops – and it doesn't clear.
B: The silver nitrate and Rochelle salt are mixed in hot water. The solution turns black.
The instructions state that the solutions are to be filtered, but I was too lazy. The precipitate eventually settles at the bottom. Other than what I have in my notes, I don't remember what I did or what happened; it didn't occur according to the instructions though. I kept the solutions in the dark in my camera cabinet and they keep pretty long; I mixed the leftover solutions maybe four months after they were mixed and they silvered the inside of the jar.
9. THE REACTION:
I placed a glass sample in a film can (of course) and poured in roughly half and half of the solutions. Ideally, one would find the time/temperature/concentration combination for a perfect 50/50 semi-silvering; but since this experiment was very rough, the final method was to pour the chemicals, wait and watch. Trial and error. I'd pull the glass out when it looked like it was getting there; if it was too much, I'd wipe the silver off with a finger (it's very easily removed), rinse and try again; or if it was too little I'd put it back in the solution. I found that agitation (swirling) did not help with the reaction (but I can't recall what it did-- uneven coating? Took longer to deposit?).
It's very difficult to get an even coating; especially when it's really half a coating of silver that you want. Keep in mind it's only a few atoms thick for it to pass light through.
It's also difficult to judge when the layer of silver is enough-- too much and your finder will be very dark; too little and you have no rangefinder patch. I had some aluminum left on the prism face (in fact, it wouldn't come off if I scrubbed), and that helped me judge when the silver was appropriately thick. Well, in theory anyways.
If the silver was too thick, it was easily removed by rubbing the surface with a finger. But for some reason, after silvering and cementing and decementing after the silver was found to be too thin, a blotch of silver stuck and would not come off.
Due to contaminants (namely, copper), the silver layer was never really silver. For my first chemical batch, it was a coppery colour, then for the second batch, it was yellowish. These tints will result in a colour cast in the finder.
As an aside, it's quite easy to make a regular (back-silvered) mirror with this method: throw a piece of glass into the solution and wait. Wipe one side, and the other side will be a nice even silver as seen through the glass, despite the unevenness or discolouration of the other (silvered) side. For other photographic uses, front-silvered mirrors are usually used, and again, this tip won't be of much use-- your reflective surface will be the 'difficult' side.
The prism to be silvered for the M2 has three optical faces, with only one requiring silvering. I taped the other surfaces so that they wouldn't be slivered.
10. CEMENTING:
Once you end up with a (barely, in my case) satisfactory semi-silvering, you can stick the beamsplitter together with water and look through it for a basic assessment. And this time, the silvering won't come off. I would look through the beamsplitter and wave a finger by the face where the RF image comes through; if the two images were about equal in brightness, then I'd go ahead for cementing. Or maybe I had it so that the reflected image was brighter? I don't remember. You'll have to experiment.
Tape up the surfaces that you don't want cement on. Apply a small drop of Canada balsam, but enough to ensure that there's enough to cover the entire surface. Then use tape or wire to hold the prisms together with the correct alignment. The correct alignment I found by looking through the beamsplitter and aligning it so that it did not skew the image; so that it was 'straight through' so to speak. Hopefully that makes some sense. In other words, if I was looking at a dot through the beamsplitter, when the beamsplitter was removed, the dot would appear to be in the same place; not above or below.
Curing the cement is usually done in an oven, but I didn't want to waste electricity so I just stuck the cemented assembly on the dashboard of one of our cars whose engine exploded last winter. A couple days in the sun at 60 degrees or more, peak, and it's solid. In fact, I tripped over a tent a couple weeks ago, camera in hand, and the rangefinder is still together and aligned. Before the re-silvering, the RF would lose alignment if you spoke condescendingly in its general direction.
11. DECEMENTING:
If you get it wrong, throw the cemented optics in acetone and they'll come apart quickly. This is also useful for cleaning any balsam that remained from before or removing excess balsam. Note that acetone removes paint, and you'll have to repaint the beamsplitter's non-optic surfaces before it goes back into the camera to reduce stray light.
mooge
Well-known
12. ALIGNING: I wrote an article about aligning an M2 rangefinder a while back and now that I've gone deeper into the hole, I've realized that I didn't understand it well previously. The beamsplitter rests against two machined rails in the rangefinder housing, and this means that the beamsplitter can not be adjusted for swing. The trouble I ran into in aligning the rangefinder was that it would not focus down to 0,7m – perhaps an error in how I decided the prisms should be cemented together (para. 10), or maybe due to a shift in other optical assemblies. To my knowledge, there is no factory information readily available on how the beamsplitter prisms should be aligned.
In the end, I couldn't solve the range issue (the closest the RF would focus was over a metre) so I angled the beamsplitter to the right. The grubscrews tend to pull the beamsplitter into alignment (i.e. Pointing straight) against the machined rails so I wedged a piece of paper in between the front prism and one of the frame walls. Crude, but it works, and that's all I need. Remember to check the range of the rangefinder with the top plate on – it limits the travel of the one of the optics and hence the minimum focusing distance.
Perhaps it's worthwhile to discuss how the beamsplitter is held in place. It rests on two rails, on the top and bottom, that are angled at 45 degrees to the viewing axis. It's held against these rails by two grubscrews, which press against a bevelled surface of the rear prism. A dab of glue in a hole on both the top and bottom of the rangefinder frame hold the prism in. Also, two spring clips hold the beamsplitter in place; on near the eyepiece and one somewhere in the middle. My recent theory is that there isn't any lateral (left-right angle) adjustability in the placement of the beamsplitter; this time when putting the beamsplitter in the rangefinder frame, it always stuck in place dictated by the grubscrews and machined rails. I was wrong last time though so I might still be wrong.
Also perhaps worth mentioning is how to remove the split beamsplitter. The front prism can be removed from the front side after removing the concave lens held in by a spring clip and spring bar. It should be loose. The rear prism can be removed by loosening the the two grubscrews (top and bottom) that hold it in place, removing one of the spring clips that presses it in place and loosening the other, and finally by pushing the prism out of the frame against the friction of the glue spots.
13. RESULTS
So with maybe $50 of materials and a lot of effort, I managed to get my M2's rangefinder back together in a workable state. It's nowhere near perfect-- the finder is very dark now (darker than my Kiev's finder), and uneven (very obviously so when it's bright outside) and tinted a disgusting dirty yellow. But it works just about as “well” as it did before – focusing in low light is difficult but possible and pretty much nothing is in focus at f/1,4. It's usable and I'm pretty happy.
In retrospect, with all that I've learned, it's probably cheaper to buy another broken camera (separated beamsplitter) than to send mine in for repair. Kind of sad, but this M2 is really beat (and now has corrosion YAY CORROSION) and will probably explode or something soon anyways.
Most important lesson learned: DON'T MESS WITH THE ALUMINUM!
14. REFERENCES, RECCOMENDED READING:
[1] http://www.make-stuff.com/formulas_&_remedies/glass_&_glasses/mirrors.html
“How to Make a Telescope”, Jean Texerau – includes a chapter on silvering methods
...Too lazy to find my other references.
And a big thank-you to everyone who contributed to a thread I made while wondering what to do once the aluminum was wiped off; and a special shout-out to fellow gearheads Vick (for his words of encouragement), Brett (for taking apart Rolleiflexes like a boss) and Roland (for putting that picture up on how to disassemble the Nokton 35).
I hope someone finds this useful (or vaguely amusing), and best of luck to you if you attempt re-silvering a mirror on your own.
15. APPENDICIES:

15.1: Separated beamsplitter.

15.2: Separated optics. Note yellowish powder, this is old balsam and it can be removed with acetone

15.3: Ruined aluminum semi-silvering. Don't do this and you'll save yourself a lot of trouble.

15.4: Glass face of silver deposit.

15.6: Air face of silver deposit. Note roughness (dull reflection) and discolouration from contaminants.

15.7: This is actually a relatively even deposit of silver.

15.8: Beamsplitter cemented and secured with tape and wire for curing.

15.9: Cemented beamsplitter after curing. There is no paint because this is my second try and I soaked the beamsplitter in acetone to get it apart.

15.10: What I mean by the machined rail. There's another one on the top of the finder frame.

15.11: Paper shims save the day again. Another example of why you shouldn't take this article too seriously.

15.12: RF optical layout sketch, assigning letters to various elements

15.13: Beamsplitter detail and attachment points

15.14: Final result. It works. Note lack of colour cast due to auto white balance.
In the end, I couldn't solve the range issue (the closest the RF would focus was over a metre) so I angled the beamsplitter to the right. The grubscrews tend to pull the beamsplitter into alignment (i.e. Pointing straight) against the machined rails so I wedged a piece of paper in between the front prism and one of the frame walls. Crude, but it works, and that's all I need. Remember to check the range of the rangefinder with the top plate on – it limits the travel of the one of the optics and hence the minimum focusing distance.
Perhaps it's worthwhile to discuss how the beamsplitter is held in place. It rests on two rails, on the top and bottom, that are angled at 45 degrees to the viewing axis. It's held against these rails by two grubscrews, which press against a bevelled surface of the rear prism. A dab of glue in a hole on both the top and bottom of the rangefinder frame hold the prism in. Also, two spring clips hold the beamsplitter in place; on near the eyepiece and one somewhere in the middle. My recent theory is that there isn't any lateral (left-right angle) adjustability in the placement of the beamsplitter; this time when putting the beamsplitter in the rangefinder frame, it always stuck in place dictated by the grubscrews and machined rails. I was wrong last time though so I might still be wrong.
Also perhaps worth mentioning is how to remove the split beamsplitter. The front prism can be removed from the front side after removing the concave lens held in by a spring clip and spring bar. It should be loose. The rear prism can be removed by loosening the the two grubscrews (top and bottom) that hold it in place, removing one of the spring clips that presses it in place and loosening the other, and finally by pushing the prism out of the frame against the friction of the glue spots.
13. RESULTS
So with maybe $50 of materials and a lot of effort, I managed to get my M2's rangefinder back together in a workable state. It's nowhere near perfect-- the finder is very dark now (darker than my Kiev's finder), and uneven (very obviously so when it's bright outside) and tinted a disgusting dirty yellow. But it works just about as “well” as it did before – focusing in low light is difficult but possible and pretty much nothing is in focus at f/1,4. It's usable and I'm pretty happy.
In retrospect, with all that I've learned, it's probably cheaper to buy another broken camera (separated beamsplitter) than to send mine in for repair. Kind of sad, but this M2 is really beat (and now has corrosion YAY CORROSION) and will probably explode or something soon anyways.
Most important lesson learned: DON'T MESS WITH THE ALUMINUM!
14. REFERENCES, RECCOMENDED READING:
[1] http://www.make-stuff.com/formulas_&_remedies/glass_&_glasses/mirrors.html
“How to Make a Telescope”, Jean Texerau – includes a chapter on silvering methods
...Too lazy to find my other references.
And a big thank-you to everyone who contributed to a thread I made while wondering what to do once the aluminum was wiped off; and a special shout-out to fellow gearheads Vick (for his words of encouragement), Brett (for taking apart Rolleiflexes like a boss) and Roland (for putting that picture up on how to disassemble the Nokton 35).
I hope someone finds this useful (or vaguely amusing), and best of luck to you if you attempt re-silvering a mirror on your own.
15. APPENDICIES:

15.1: Separated beamsplitter.

15.2: Separated optics. Note yellowish powder, this is old balsam and it can be removed with acetone

15.3: Ruined aluminum semi-silvering. Don't do this and you'll save yourself a lot of trouble.

15.4: Glass face of silver deposit.

15.6: Air face of silver deposit. Note roughness (dull reflection) and discolouration from contaminants.

15.7: This is actually a relatively even deposit of silver.

15.8: Beamsplitter cemented and secured with tape and wire for curing.

15.9: Cemented beamsplitter after curing. There is no paint because this is my second try and I soaked the beamsplitter in acetone to get it apart.

15.10: What I mean by the machined rail. There's another one on the top of the finder frame.

15.11: Paper shims save the day again. Another example of why you shouldn't take this article too seriously.

15.12: RF optical layout sketch, assigning letters to various elements

15.13: Beamsplitter detail and attachment points

15.14: Final result. It works. Note lack of colour cast due to auto white balance.
mooge
Well-known
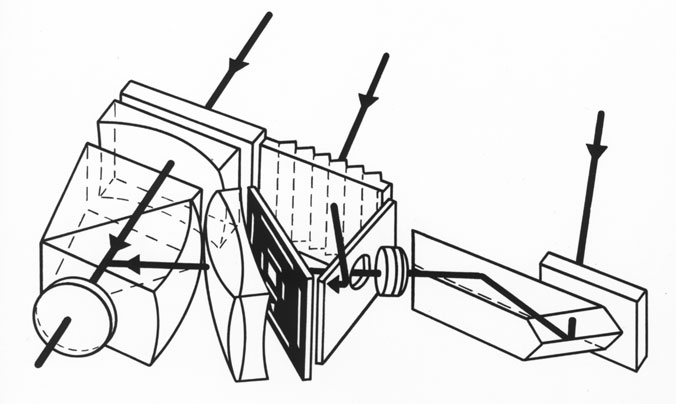
BONUS!!!
real RF diagram. from summilux.net (I think it's a scan from a brochure?):
http://www.summilux.net/m_system/m2.html
sanmich
Veteran
wow!
You get my admiration for
1- going through this
2- going through this successfully
but...
Luton is resilvering M3 prisms, because there are no parts anymore.
The 0.72 RF, as far as I know has been kept almost unchanged since the M2, which makes parts easily available. I would guess DAG could have provided one.
which doesn't diminish your success in any way (I'm guess it's important for M3 owner to see this...)
You get my admiration for
1- going through this
2- going through this successfully
but...
Luton is resilvering M3 prisms, because there are no parts anymore.
The 0.72 RF, as far as I know has been kept almost unchanged since the M2, which makes parts easily available. I would guess DAG could have provided one.
which doesn't diminish your success in any way (I'm guess it's important for M3 owner to see this...)
Jack Conrad
Well-known
Totally Awesome Cheapskatery.
LOVE the presentation.
mooge
Well-known
I actually never thought of trying to get parts from DAG or elsewhere-- that's probably not such a bad idea. I'm not too sure anyone would have one though, and if they did, it's probably not cheap.
Cheapskatery it is, but I had a 2 month trip coming up so it had to get done. I took my time repairing it (3 months? 4 months?) but sending it out could have taken longer, I suspect.
Cheapskatery it is, but I had a 2 month trip coming up so it had to get done. I took my time repairing it (3 months? 4 months?) but sending it out could have taken longer, I suspect.
R
rick oleson
Guest
Congratulations, this is very impressive. Are you seriously only 21? If so, you will be very skilled indeed by the time you reach my age (if by some complete miracle you should manage to live so long)
nobbylon
Veteran
superb! I love this kind of attitude. Instead of throwing cash at it, figure it out and DIY. nicely done.
R
rick oleson
Guest
I also really like the photo, with the autumn leaves on top of the electronic keyboard. Introduces all sorts of silent questions into the mind......
ChrisLivsey
Veteran
Wonderful !!
Many thanks, my M2 is at Luton as I speak undergoing this procedure, you have fully confirmed I made the right decision
Many thanks, my M2 is at Luton as I speak undergoing this procedure, you have fully confirmed I made the right decision
mooge
Well-known
Seriously only 21. kind of interesting to get feedback from you, Rick; your website was one a few that I referred to when I was learning how to repair cameras.
I guess in this case, you can't really compare my DIY solution and getting it done properly. This is more of a hack just to get it working, the end result is much dimmer and dirtier than the viewfinder should be. I suppose though if you're patient and precise with the chemistry, you could get a reasonably good result using the same methods. It's not like replacing a shutter curtain where the result will be the same regardless of who does it; silver deposition like this will always be inferior to properly done CVD (as far as I understand anyways).
I guess in this case, you can't really compare my DIY solution and getting it done properly. This is more of a hack just to get it working, the end result is much dimmer and dirtier than the viewfinder should be. I suppose though if you're patient and precise with the chemistry, you could get a reasonably good result using the same methods. It's not like replacing a shutter curtain where the result will be the same regardless of who does it; silver deposition like this will always be inferior to properly done CVD (as far as I understand anyways).
Seriously only 21. kind of interesting to get feedback from you, Rick; your website was one a few that I referred to when I was learning how to repair cameras.
I guess in this case, you can't really compare my DIY solution and getting it done properly. This is more of a hack just to get it working, the end result is much dimmer and dirtier than the viewfinder should be. I suppose though if you're patient and precise with the chemistry, you could get a reasonably good result using the same methods. It's not like replacing a shutter curtain where the result will be the same regardless of who does it; silver deposition like this will always be inferior to properly done CVD (as far as I understand anyways).
You've gained much knowledge through experience and you can't over estimate the value of that, and thanks for sharing your experiences with us, it has been a fascinating read.
Cheers,
Brett
Jerevan
Recycled User
Great write-up and a good job! 
As an aside, the UV cement can be really tricky, if you need to split the parts again, and it sets much quicker too. Canada balsam is much easier to handle.
Where did you get the balsam? I am looking for some.
As an aside, the UV cement can be really tricky, if you need to split the parts again, and it sets much quicker too. Canada balsam is much easier to handle.
Where did you get the balsam? I am looking for some.
It's out there, and cheaply enough if you avoid the big medical/lab suppliers...here's a link to an ebay listing (in Canada, of course). Enough to do dozens of prisms.Great write-up and a good job!
As an aside, the UV cement can be really tricky, if you need to split the parts again, and it sets much quicker too. Canada balsam is much easier to handle.
Where did you get the balsam? I am looking for some.
Cheers,
Brett
Jerevan
Recycled User
Brett,
thank you very much for the tip!
I still have some left, but maybe it's a good time to stock up.
thank you very much for the tip!
I still have some left, but maybe it's a good time to stock up.
Welcome. You're probably right. It can be feast or famine on ebay with the stuff, it is not always on offer at reasonable prices and worth putting some aside when it appears at a decent price.Brett,
thank you very much for the tip!
I still have some left, but maybe it's a good time to stock up.
Cheers,
Brett
R
rick oleson
Guest
"Seriously only 21..."
Very impressed. I didn't even begin to tinker with this stuff until I was into my mid-20s.
I have a very sharp nephew in British Columbia. I guess maybe the really smart ones are either born in Canada or move there......
: ) =
Very impressed. I didn't even begin to tinker with this stuff until I was into my mid-20s.
I have a very sharp nephew in British Columbia. I guess maybe the really smart ones are either born in Canada or move there......
: ) =
Vickko
Veteran
Good work, nice writeup.
hans voralberg
Veteran
Hats off to you! Amazing stuff.
daveleo
what?
I don't have the slightest interest in repairing a rangefinder camera, but this is a fantastic piece of work and write-up that you completed.
Wicked excellent ! !
Wicked excellent ! !
Share:
-
This site uses cookies to help personalise content, tailor your experience and to keep you logged in if you register.
By continuing to use this site, you are consenting to our use of cookies.