Guth
Appreciative User
The grain in the birdseye maple that was used in the construction of this guitar is quite stunning — an added dimension is revealed when viewing the guitar while moving it around. Success at capturing the grain in a photo is very dependent on the angle from which the images are taken. Of course I can't see any of this when actually playing the guitar.


maggieo
More Deadly
Oh, lordy! That must sing like an angel.
markjwyatt
Well-known
D
Deleted member 65559
Guest
At the request of RHL (Oregon).... more guitars. My 1936 Martin D18: 1 of 268 from that year.
IMG_8693 by /url], on Flickr

D
Deleted member 65559
Guest
Oh, lordy! That must sing like an angel.
Yes it does!
raydm6
Yay! Cameras! 🙈🙉🙊┌( ಠ_ಠ)┘ [◉"]
D
Deleted member 65559
Guest
rhl-oregon, davidnewtonguitars & Guth, since we mentioned Bill Collings, here's a photo of a Collings D1avvarnish (Dreadnaught, mahogany back & sides, Adirondack (red spruce) top, vintage '30s dimension neck, varnish finish 2009:
IMG_8402 copy (1) by , on Flickr

davidnewtonguitars
Family Snaps
Recent video shoot for my latest guitar.
Why not let this thread be our "guitar cafe" ? It will save confusion on my part for sure!
Why not let this thread be our "guitar cafe" ? It will save confusion on my part for sure!


Yokosuka Mike
Abstract Clarity
Sigma Sd Quattro
Sigma 17-70mm f2.8-4 DC "Contemporary" lens (25mm-105mm on Sd Quattro)
Yokohama, Japan - October, 2019
A live performance by "Gypsy Groove" in Yokohama Park (October 20, 2019).
These guys were really good. When they played "Volare" everyone in the crowd sang along with them - in Spanish!
All the best,
Mike
Sigma 17-70mm f2.8-4 DC "Contemporary" lens (25mm-105mm on Sd Quattro)
Yokohama, Japan - October, 2019
A live performance by "Gypsy Groove" in Yokohama Park (October 20, 2019).
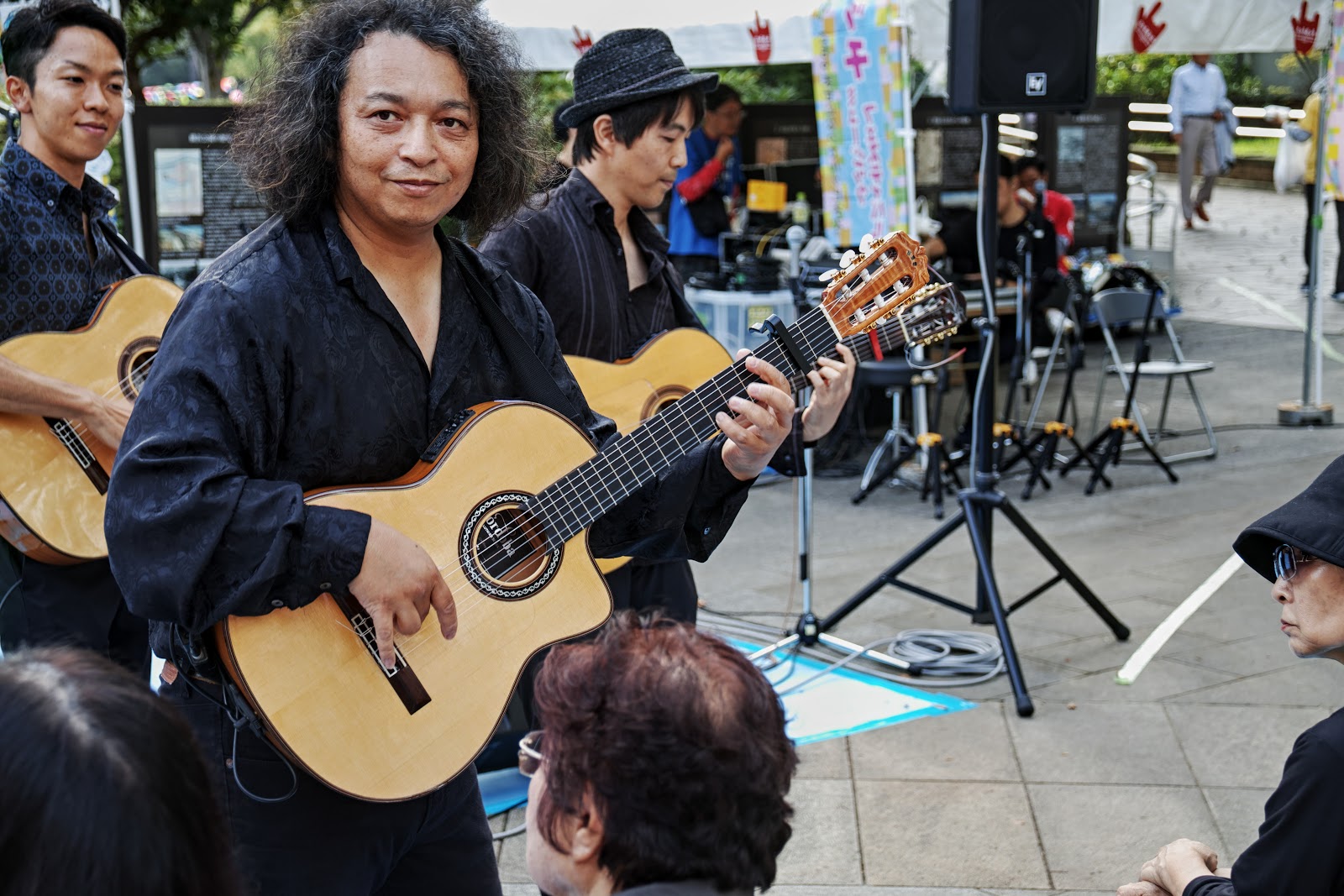
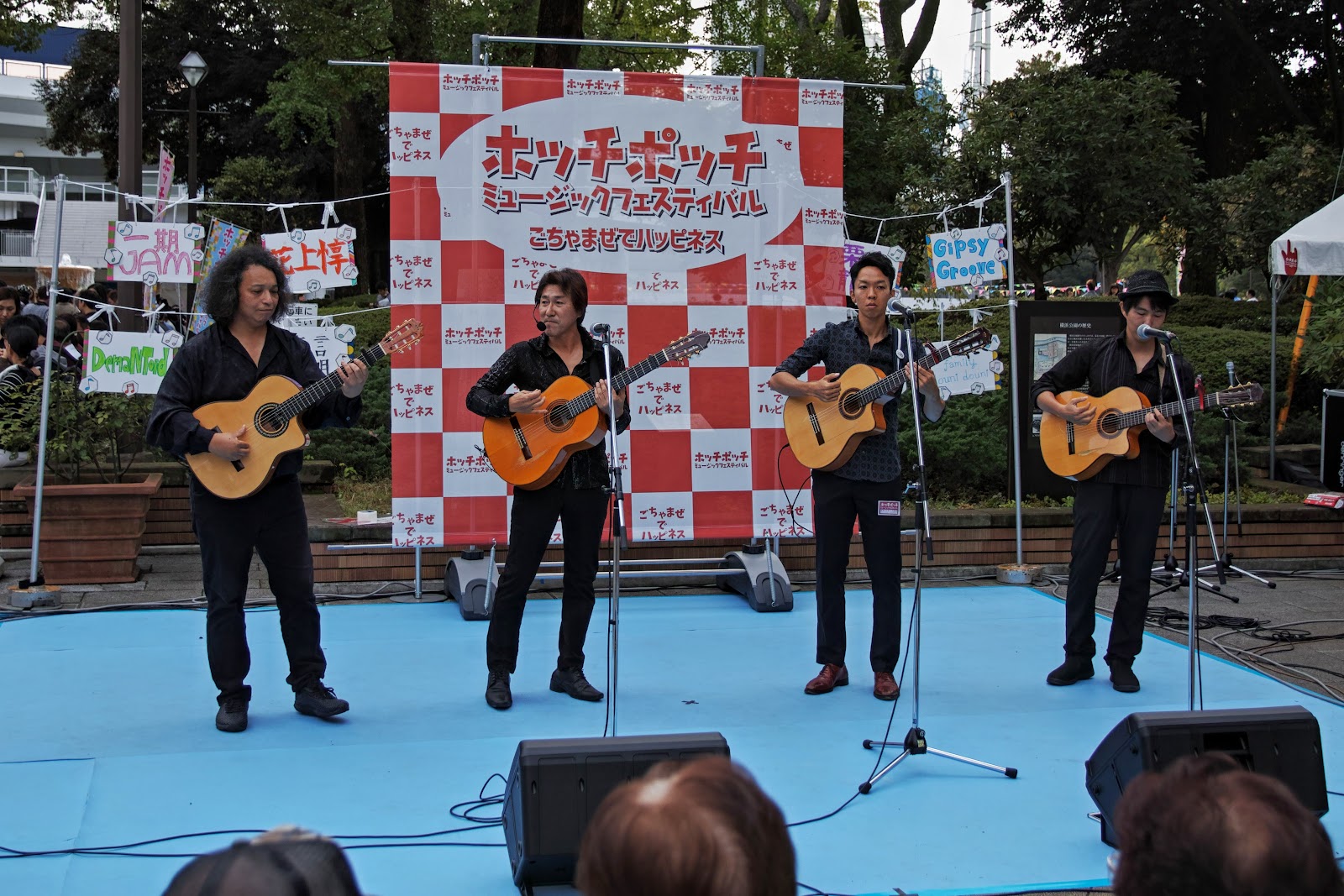
These guys were really good. When they played "Volare" everyone in the crowd sang along with them - in Spanish!
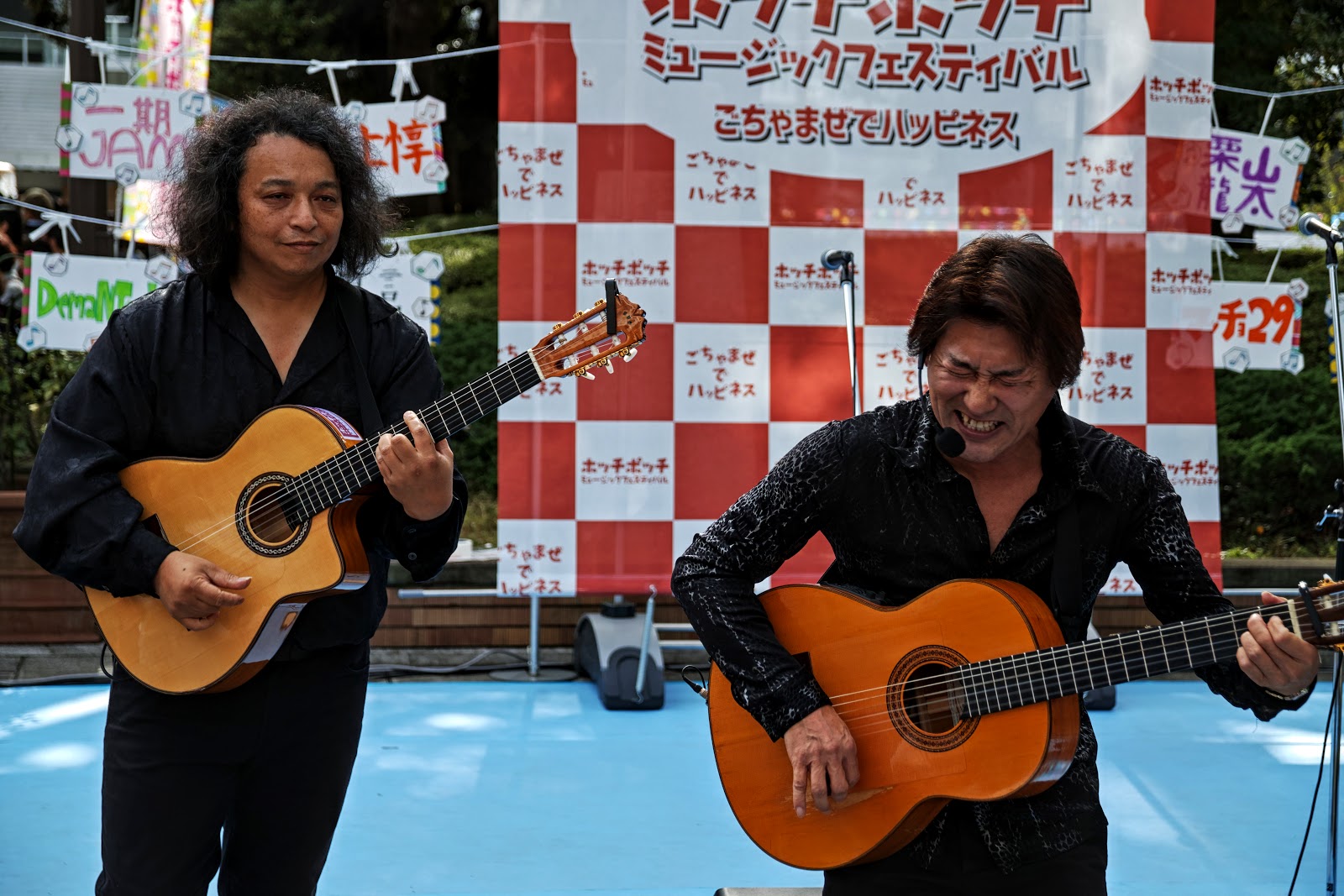
All the best,
Mike
davidnewtonguitars
Family Snaps
I said I would tell my Bill Collings story here:
In 1975 I set up a guitar shop in my brother's living room in Beaumont, TX. I was searching around for local guitar builders and connected with Bill, who was living in Houston, working at a big machine shop and building his guitars in a two bedroom apartment, the 2nd bedroom being his shop. I visited him a lot after that, he was very encouraging to me because I was actually building, not just talking about it. There were others in Houston we would visit together and compare work. He moved into a big house in the Montrose, along with a Dulcimer builder. The downstairs rooms were woodshops, living was upstairs.
He built Lyle Lovett's first guitar there, bought a 911S, and proceeded to blow the engine shortly thereafter, driving crazy, which was Bill's way. He & I were both unmarried and were free to go to the clubs and hear the guitar guys, it was all "progressive country" at that time.
Bill always talked about how to build more and more guitars at a time by machine methods, while I wanted to build by hand with as few machines as possible. That is the reason we never "partnered up". I visited Bill when he built first large shop in Dripping Springs, he tried to entice me to join him there, but it was not to be. I think he was doing 25 guitars a month at that time, and was beginning to travel a lot, hand picking his wood stocks.
When I think about Bill, and early days, I remember his dual nature, when he was working he demanded perfection of himself and others, when he was not working, he was carefree, funny, and almost a risk taker. He always encouraged me to develop each step of the guitar building process and how to effect the sound and playability of the finished guitar.
In 1975 I set up a guitar shop in my brother's living room in Beaumont, TX. I was searching around for local guitar builders and connected with Bill, who was living in Houston, working at a big machine shop and building his guitars in a two bedroom apartment, the 2nd bedroom being his shop. I visited him a lot after that, he was very encouraging to me because I was actually building, not just talking about it. There were others in Houston we would visit together and compare work. He moved into a big house in the Montrose, along with a Dulcimer builder. The downstairs rooms were woodshops, living was upstairs.
He built Lyle Lovett's first guitar there, bought a 911S, and proceeded to blow the engine shortly thereafter, driving crazy, which was Bill's way. He & I were both unmarried and were free to go to the clubs and hear the guitar guys, it was all "progressive country" at that time.
Bill always talked about how to build more and more guitars at a time by machine methods, while I wanted to build by hand with as few machines as possible. That is the reason we never "partnered up". I visited Bill when he built first large shop in Dripping Springs, he tried to entice me to join him there, but it was not to be. I think he was doing 25 guitars a month at that time, and was beginning to travel a lot, hand picking his wood stocks.
When I think about Bill, and early days, I remember his dual nature, when he was working he demanded perfection of himself and others, when he was not working, he was carefree, funny, and almost a risk taker. He always encouraged me to develop each step of the guitar building process and how to effect the sound and playability of the finished guitar.
rhl-oregon
Cameras Guitars Wonders
Well, I’m glad to see y’all who were recently hijacking the Erwin Puts kerfuffle thread stepping up here with eye candy and guitar stories and players. David, that’s an illuminating story about Mr Collings and how his scaling-up approach confirmed in some way your conviction about keeping your lutherie more personal.
Here is a North Carolina songwriter I recently worked with, Laurelynn Dossett, with her Collings.
And songwriter Anya Hinkle with a roadworn Gibson almost her size.
I don’t know what bass Johnny Calamari is playing, but this ain’t no bass thread.
Here is a North Carolina songwriter I recently worked with, Laurelynn Dossett, with her Collings.
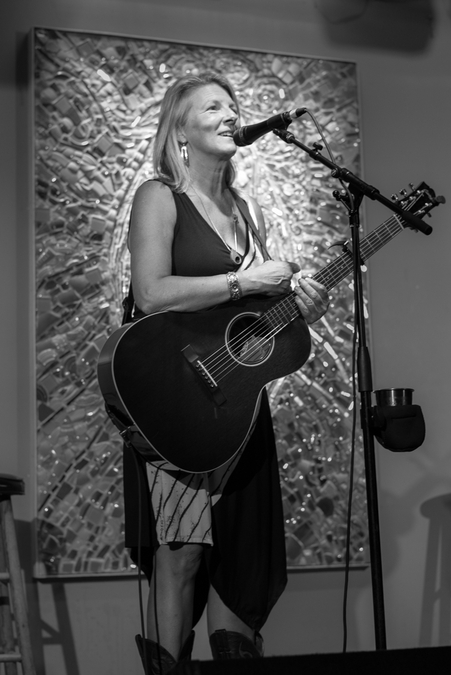
And songwriter Anya Hinkle with a roadworn Gibson almost her size.
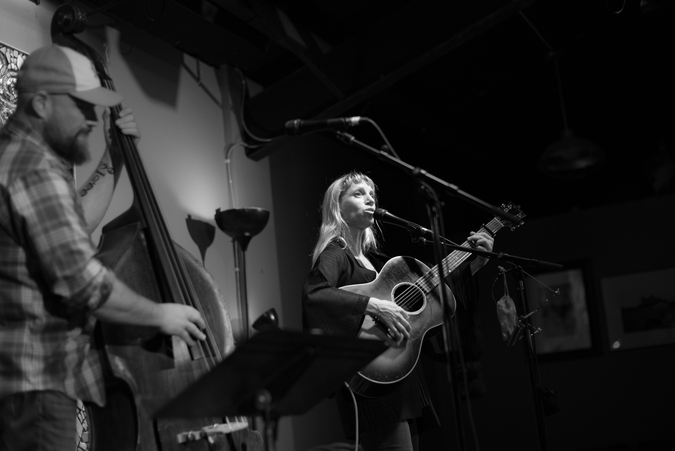
I don’t know what bass Johnny Calamari is playing, but this ain’t no bass thread.
rhl-oregon
Cameras Guitars Wonders
These older gentlemen, brothers I suspect, played a set of old time and gospel at Jackson Springs day, not far from here. In more ways than one they are very close to the bosom of Abraham.
Here is a younger member of their cohort. The light was good inside the old train depot/post office.
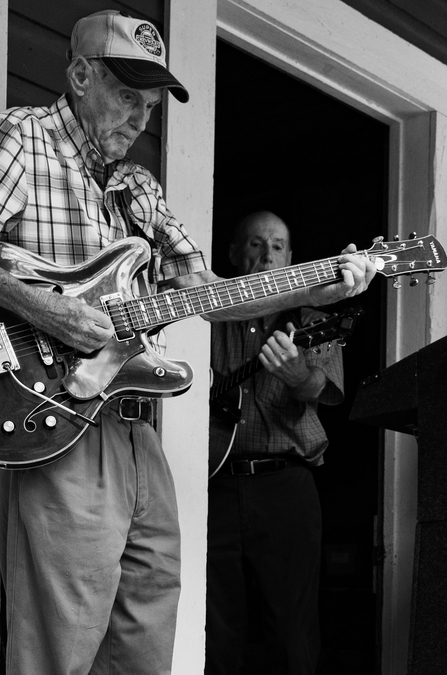
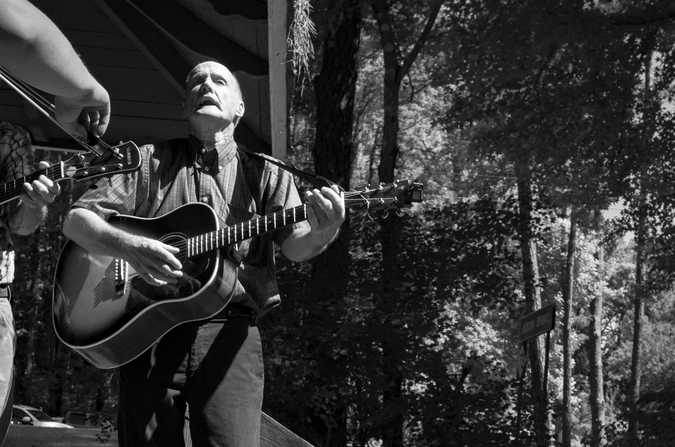
Here is a younger member of their cohort. The light was good inside the old train depot/post office.
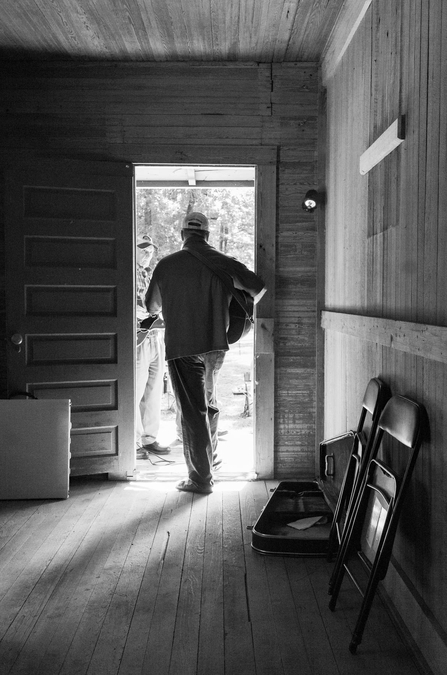
rhl-oregon
Cameras Guitars Wonders
Puerto Vallarta. Who built this guitar? The American ladies don’t care. (Neither did I.)
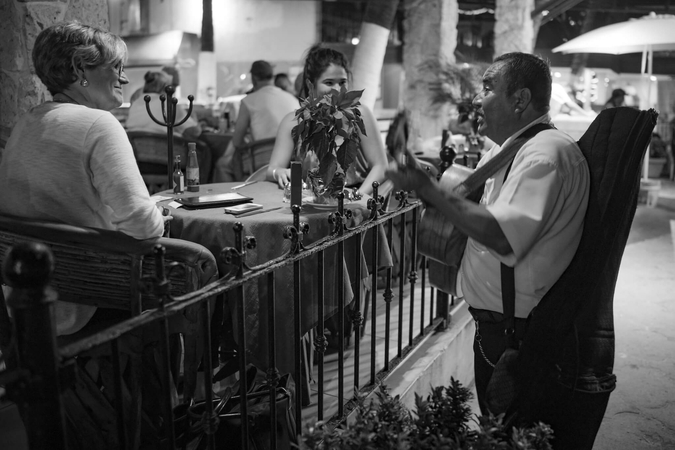
rhl-oregon
Cameras Guitars Wonders
Some of the musicians playing at the wake of Bob November, longtime guitar hawk, owner of McKenzie River Music in Eugene, Oregon, and Leicaphile. He owned an M6 but was talking with me about getting an M9 the last time I saw him. I was using (and recommending) the Ricoh GXR & M module (which I used for this image with a ZM 50/2). He went upstairs at the shop and brought me the last of his film—25-30 rolls of TMax and Ektar and Portra.

davidnewtonguitars
Family Snaps
Thanks Robert. I can build guitars, but your pictures tell stories.
charjohncarter
Veteran
I'll put this one up. I bought this guitar at a WigWam Store in Beaverton, Oregon in about 1965 ($25). I had many guitars before I bought this; it is the first one I bought at a store. It is called a Decca and 'made in Japan.' I still play it: sometimes the old tools work the best.
But I wish I had one of David's hand mades. Do yourself a favor and look at his website: beautiful.
Decca Guitar 1965c by John Carter, on Flickr
But I wish I had one of David's hand mades. Do yourself a favor and look at his website: beautiful.

Guth
Appreciative User
Robert, thank you for prompting the move to this thread. As always, I love your photos. I especially enjoyed the series of the likely brothers. The shot taken from inside of the depot in particular is just wonderful.
Deardorff38, be they vintage or modern those are some great guitars that you have. Thanks for sharing your photos. Would you happen to have any recordings of them posted up anywhere on the web?
David, thanks for remembering to share your story about Bill. I would love to hear any others that you might have time to share. I'm curious to know if you happened to cross paths with Guy Clark back then. I don't know if he was already building guitars by that point in time but perhaps he was doing some repair work by then. By the way, how did your video turn out?
Deardorff38, be they vintage or modern those are some great guitars that you have. Thanks for sharing your photos. Would you happen to have any recordings of them posted up anywhere on the web?
David, thanks for remembering to share your story about Bill. I would love to hear any others that you might have time to share. I'm curious to know if you happened to cross paths with Guy Clark back then. I don't know if he was already building guitars by that point in time but perhaps he was doing some repair work by then. By the way, how did your video turn out?
Yokosuka Mike
Abstract Clarity
Panasonic DMC-GX7, Sigma 60mm f2.8 lens
Yokohama, Japan - Yoshida-cho street party
Sometimes it's good to be a guitar player in a band!
All the best,
Mike
Yokohama, Japan - Yoshida-cho street party
Sometimes it's good to be a guitar player in a band!
All the best,
Mike
Guth
Appreciative User
While I like David's far more personal story involving Bill Collings better than mine, I do feel fortunate to have one of my own to share. I first met Bill back in 1991 after leaving my job in Dallas and moving to Austin. Other than the fact that I no longer desired a career in engineering I had no clue what I wanted to do. Fortunately I had saved up a fair amount of money and had some time to figure it out. I thought it would be cool to build acoustic guitars and was hoping to land a job with Bill. So even though I had absolutely no woodworking skills (but I do love guitars) I just showed up at his shop offering him two weeks of my time for free as sort of a trial period.
As I mentioned over in the Putts thread, Bill was so busy at that point that he couldn't take me up on my offer — he simply didn't have the time to show me what it was that he could us my help with. Bill did take the time to show me around his shop along with a few of his guitars. He was also kind enough to lend me a few of his books on guitar building that he kept around. To my surprise I did eventually receive a job offer some time later. Collings Guitars was growing and had relocated to a larger facility outside of Austin (the one that David mentioned). By then I had already started a new career in marketing communications and was actually enjoying my work. So (hangs head) I turned down the chance to work at Collings Guitars.
The small nest egg that I had arrived in Austin with didn't last forever but by 1995 I had managed to save up enough money to be able to buy a Collings guitar for myself. I had also turned a friend of mine (a far, far better player than myself) on to Bill's guitars. Eventually we each ended up having a guitar custom made for us. It was somewhat unfortunate that I had become enamored with rosewood at that time as I would later discover that I am a mahogany guy at heart so that guitar is no longer with me. I'm saddened just a bit by that fact for the first time ever as I look back at these images. (It has been well over twenty years since I last viewed the slides that I made these scans from.) It had gotten to the point where the guitar just wasn't being played. Realizing just how much work actually goes into building a guitar that seemed like a real shame. In 2012 I ended up trading it to someone that would play it and appreciate it.
Anyway, when my buddy and I were having our guitars built the crew out at Collings were great. The allowed us stop by often to check in on the guitars as they evolved over time through the various stages of the build and answered a nearly endless amount of questions. My friend and I took photos of each other to document the experience. Sadly I have just a handful of images. My apologies as I rushed the scanning of the slides just so I could share here. But they at least they do contain "guitar content" and provide a tiny glimpse into the state of Collings guitars circa 1995. While I did then, and still do, find it all to be very fascinating, looking at myself in these photos it strikes me that this all took place much longer ago than I realized. Time flies as they say. With that in mind, David, please feel free to correct me if I bungle any the details pertaining to the work involved.
These are matched sets of sides that are waiting for the next phase of the build process. Here they already have the side braces along with the kerfing glued up. The kerfing provides greater support at the point where the top and back of the be attached to the sides. Here you can see that the guitar-to-be serial number has already been affixed. They also mark the top, back, neck, etc. with the same serial number so that all of the pre-chosen components can be easily identified for assembly. (My guitar was to be serial number 2051.)
We got to pick out the wood blanks to be used in the construction of the guitars. Here is the top of the guitar with the set of spruce that I chose. Just as the sides match, so too do the top and back of the guitar that are made up of a piece of wood that has been split in half and bookmatched — after the quartersawn wood is split in half it is opened up like a book before being glued together to form a single piece. As seen in this photo mine was to be an OM guitar, the same sized body as used in a 000 guitar. My buddy had a larger dreadnaught sized guitar made for him.
This is rosewood back for the guitar. Here you can see the bookmatched effect where the grain on each side of the split piece of wood mirrors that of the other. The two pieces are separated by a lighter strip of purfling (made up of very small pieces of wood set in a decorative pattern).
Here is the flip-side of the back of the guitar. The bracing pieces have already been attached with glue. As with the top of the guitar, the braces will be carved before the body of the guitar is fully assembled. This is part of what gives the guitar it's voice.
Lastly, this image is from a later visit to the shop. Here you can see the body of my guitar resting on it's side after the assembly of the pieces appearing in the previous photos has been completed. Soon the neck of the guitar will be attached to the body.
Sorry for the extremely lengthy post. Obviously photography gear isn't the only thing that people can geek out over.
As I mentioned over in the Putts thread, Bill was so busy at that point that he couldn't take me up on my offer — he simply didn't have the time to show me what it was that he could us my help with. Bill did take the time to show me around his shop along with a few of his guitars. He was also kind enough to lend me a few of his books on guitar building that he kept around. To my surprise I did eventually receive a job offer some time later. Collings Guitars was growing and had relocated to a larger facility outside of Austin (the one that David mentioned). By then I had already started a new career in marketing communications and was actually enjoying my work. So (hangs head) I turned down the chance to work at Collings Guitars.
The small nest egg that I had arrived in Austin with didn't last forever but by 1995 I had managed to save up enough money to be able to buy a Collings guitar for myself. I had also turned a friend of mine (a far, far better player than myself) on to Bill's guitars. Eventually we each ended up having a guitar custom made for us. It was somewhat unfortunate that I had become enamored with rosewood at that time as I would later discover that I am a mahogany guy at heart so that guitar is no longer with me. I'm saddened just a bit by that fact for the first time ever as I look back at these images. (It has been well over twenty years since I last viewed the slides that I made these scans from.) It had gotten to the point where the guitar just wasn't being played. Realizing just how much work actually goes into building a guitar that seemed like a real shame. In 2012 I ended up trading it to someone that would play it and appreciate it.
Anyway, when my buddy and I were having our guitars built the crew out at Collings were great. The allowed us stop by often to check in on the guitars as they evolved over time through the various stages of the build and answered a nearly endless amount of questions. My friend and I took photos of each other to document the experience. Sadly I have just a handful of images. My apologies as I rushed the scanning of the slides just so I could share here. But they at least they do contain "guitar content" and provide a tiny glimpse into the state of Collings guitars circa 1995. While I did then, and still do, find it all to be very fascinating, looking at myself in these photos it strikes me that this all took place much longer ago than I realized. Time flies as they say. With that in mind, David, please feel free to correct me if I bungle any the details pertaining to the work involved.

These are matched sets of sides that are waiting for the next phase of the build process. Here they already have the side braces along with the kerfing glued up. The kerfing provides greater support at the point where the top and back of the be attached to the sides. Here you can see that the guitar-to-be serial number has already been affixed. They also mark the top, back, neck, etc. with the same serial number so that all of the pre-chosen components can be easily identified for assembly. (My guitar was to be serial number 2051.)

We got to pick out the wood blanks to be used in the construction of the guitars. Here is the top of the guitar with the set of spruce that I chose. Just as the sides match, so too do the top and back of the guitar that are made up of a piece of wood that has been split in half and bookmatched — after the quartersawn wood is split in half it is opened up like a book before being glued together to form a single piece. As seen in this photo mine was to be an OM guitar, the same sized body as used in a 000 guitar. My buddy had a larger dreadnaught sized guitar made for him.

This is rosewood back for the guitar. Here you can see the bookmatched effect where the grain on each side of the split piece of wood mirrors that of the other. The two pieces are separated by a lighter strip of purfling (made up of very small pieces of wood set in a decorative pattern).

Here is the flip-side of the back of the guitar. The bracing pieces have already been attached with glue. As with the top of the guitar, the braces will be carved before the body of the guitar is fully assembled. This is part of what gives the guitar it's voice.

Lastly, this image is from a later visit to the shop. Here you can see the body of my guitar resting on it's side after the assembly of the pieces appearing in the previous photos has been completed. Soon the neck of the guitar will be attached to the body.
Sorry for the extremely lengthy post. Obviously photography gear isn't the only thing that people can geek out over.
davidnewtonguitars
Family Snaps
Thanks Guth, great shots from the shop.
Share:
-
This site uses cookies to help personalise content, tailor your experience and to keep you logged in if you register.
By continuing to use this site, you are consenting to our use of cookies.